
April 2025: Construction Materials Price Report
Lumber Prices Surge—Defending Against 2025’s Cost Hikes
Lumber prices surged 17.2% year-over-year in early 2025, reaching $486 per 1,000 board feet, driven by tariff fears, supply chain disruptions, and strong housing demand. Construction input costs are now 40.5% above pre-pandemic levels. Contractors locked into fixed-price contracts face squeezed margins as material costs spike. Proactive strategies such as incorporating escalation clauses, bulk purchasing, and exploring alternative materials are essential to protect budgets. At Paragon, we help clients anticipate these shifts and secure materials early to maintain predictable outcomes amid volatile markets.
Continue reading this article.
“Golden Age” or Tariff-Driven Recession?
ENR’s Top 425 Owners saw construction-in-progress rise 9.3% to $595.8 billion from 2023 to 2024, buoyed by moderately sized projects as megaprojects mature. Yet labor growth is stalling, and President Trump’s new tariffs—up to 50% reciprocal duties on imports from 90 countries—triggered a $5 trillion market loss in two days. University project managers describe adapting to market shifts as “like turning a battleship.” Experts warn a recession may already have begun. Owners are prioritizing early procurement, flexible contracts, and alternative designs to manage rising costs and uncertainty. Paragon helps clients navigate this volatile “golden age” with strategic planning and collaboration.
Continue reading this article.
Wildfire Recovery in Los Angeles
The January 2025 wildfires destroyed over 16,000 structures in Los Angeles, causing up to $54 billion in damage and displacing thousands. Rebuilding faces labor shortages, supply chain constraints, and insurance challenges. Fire-resistant materials like steel and fiber cement reduce vulnerability by 60%, while modular robotics such as Concert accelerate reconstruction and improve safety. Permitting timelines have been cut from 120 to 45 days. Coordinated debris removal and community rebuilding authorities are critical for recovery. Paragon’s disaster recovery expertise emphasizes detailed planning, transparent communication, and flexible phased delivery to build a more resilient future.
Continue reading this article.
Preparing for Recession — How Construction Can Stay Resilient in 2025
Sixty percent of CFOs predict a recession in 2025 amid tariffs, inflation, and rising interest rates. Construction input prices are up 40.5% since 2020, while labor shortages demand 439,000 new workers this year. Firms are adopting phased project approaches, diversified supply chains, and AI-driven cost tracking to mitigate risk. Modular robotics like Concert fill labor gaps by handling repetitive tasks, enhancing safety and efficiency. Anirban Basu cautions tariffs are “medicine” that may strain the industry. Paragon guides clients through scenario planning, flexible contracts, and technology adoption to thrive amid economic uncertainty.
Continue reading this article.
Conclusion
The construction industry in 2025 is facing a series of interconnected challenges—tariffs, rising material costs, labor shortages, and supply chain disruptions—that are more than just obstacles; they’re signals of a fundamental shift. Tariffs on steel, aluminum, and other key materials are inflating prices at a rate not seen in years, forcing contractors to revisit pricing models, renegotiate contracts, and explore alternative sourcing strategies. Meanwhile, automation and AI-driven robotics like Concert are beginning to reshape job sites, filling critical labor gaps and making projects safer and more efficient. At the same time, global trade tensions and domestic policy uncertainties are creating volatile markets, with supply chains strained and costs unpredictable. Every project now requires proactive planning, flexible procurement, and innovative solutions to stay on schedule and within budget. The companies that will thrive aren’t waiting for stability—they’re leading by adapting quickly, leveraging technology, and forging resilient supply partnerships. But perhaps the greatest risk isn’t rising costs—it’s inaction. This is a moment for bold, data-informed decisions rooted in discipline and foresight. The industry’s future belongs to those who see disruption as an opportunity to innovate, to build smarter, and to lead with purpose. At Paragon Construction Consulting, we believe this is a defining moment—one where strategic action and unwavering focus will set the standard for the next generation of construction. Let’s build that future—together.
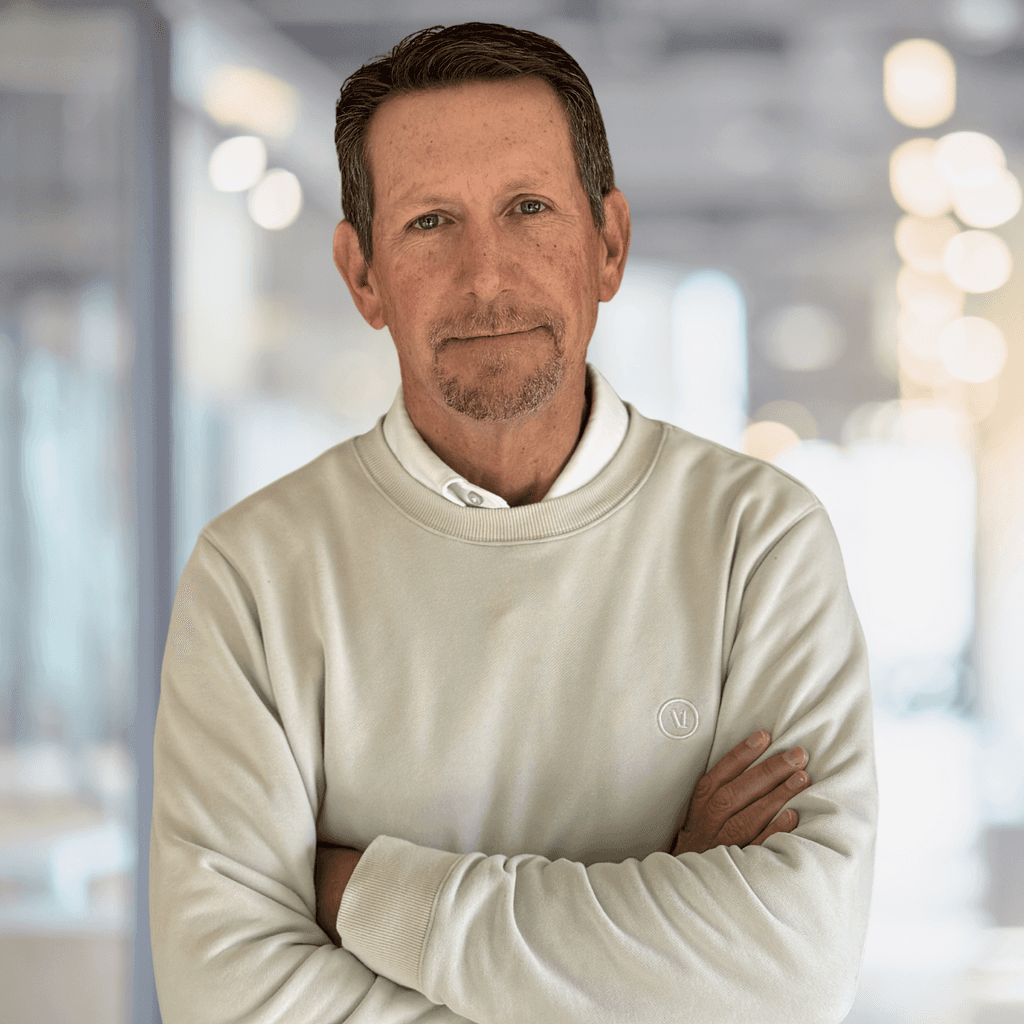
Jeff Hall
President & CEO
Online
Get in Touch
Commodity
12 Month % Change
1 Month % Change
Softwood Lumber
+12.6
+4.7
Hardwood Lumber
+1.0
+6.6
General Millworks
+0.9
-0.1
Soft Plywood Products
-6.1
+0.6
Hot Rolled Steel
-11.4
+2.3
Copper Wire & Cable
+12.7
+5.5
Power Wire & Cable
+5.2
+2.2
Builder's Hardware
+2.9
+0.6
Plumbing Fixtures
+2.6
0.0
Furnaces and Heaters
-0.4
+0.3
Sheet Metal Products
+1.3
+1.5
Electrical Lighting Fixtures
+3.1
+0.3
Nails
-3.7
0.0
Major Appliances
-0.4
-0.1
Ready-Mix Concrete
+0.5
-0.4
Asphalt Roofing & Siding
-0.6
-0.2
Gypsum Products
+1.8
0.0
Insulation
+5.6
+0.6
Contractor Confidence Crashes Amid Tariff Chaos
Contractor confidence hit a three-year low in early 2025 as tariffs on steel and aluminum drove construction input prices up 1.4% in January—the largest jump in two years. Labor growth slowed to 1.8% year-over-year, the weakest in four years, while 80% of contractors faced tariff-related price hikes and 20% paused projects. Firms are responding with shorter bid windows, stronger supplier partnerships, and real-time cost tracking. Anirban Basu warns tariffs could stall nearly $600 billion in construction-in-progress. Paragon advises agile procurement and risk-sharing contracts to navigate this uncertainty.
Continue reading this article.
20-City Average Cost Indexes, Wages, Prices
ENR publishes both a Construction Cost Index and Building Cost index that reports the average national price by surveying 20 major cities across the United States. These figures report the national average change of cost over the last month.
CONCRETE BLOCK
+1.1%
READY MIX CONCRETE
0.0
ASPHALT PAVING
-0.3
PORTLAND CEMENT
+6.9
ALUMINIUM SHEET
+0.1%
REINFORCING BARS
-1.5%
WIDE FLANGE
+0.4%
STAINLESS-STEEL SHEET
+3.3%
CORRUGATED-STEEL PIPE
-1.2%
DUCTILE-IRON PIPE
+2.5%
PVC WATER PIPE
+0.6%
REINFORCED CONCRETE PIPE
-2.2%
GYPSUM WALLBOARD
-0.3%
PARTICLE BOARD
+1.2%
PLYWOOD
+1.5%
LUMBER
+2.0%
Sources
Paragon compiles the latest and most accurate information. It’s worth noting, some sources release data more or less frequently.
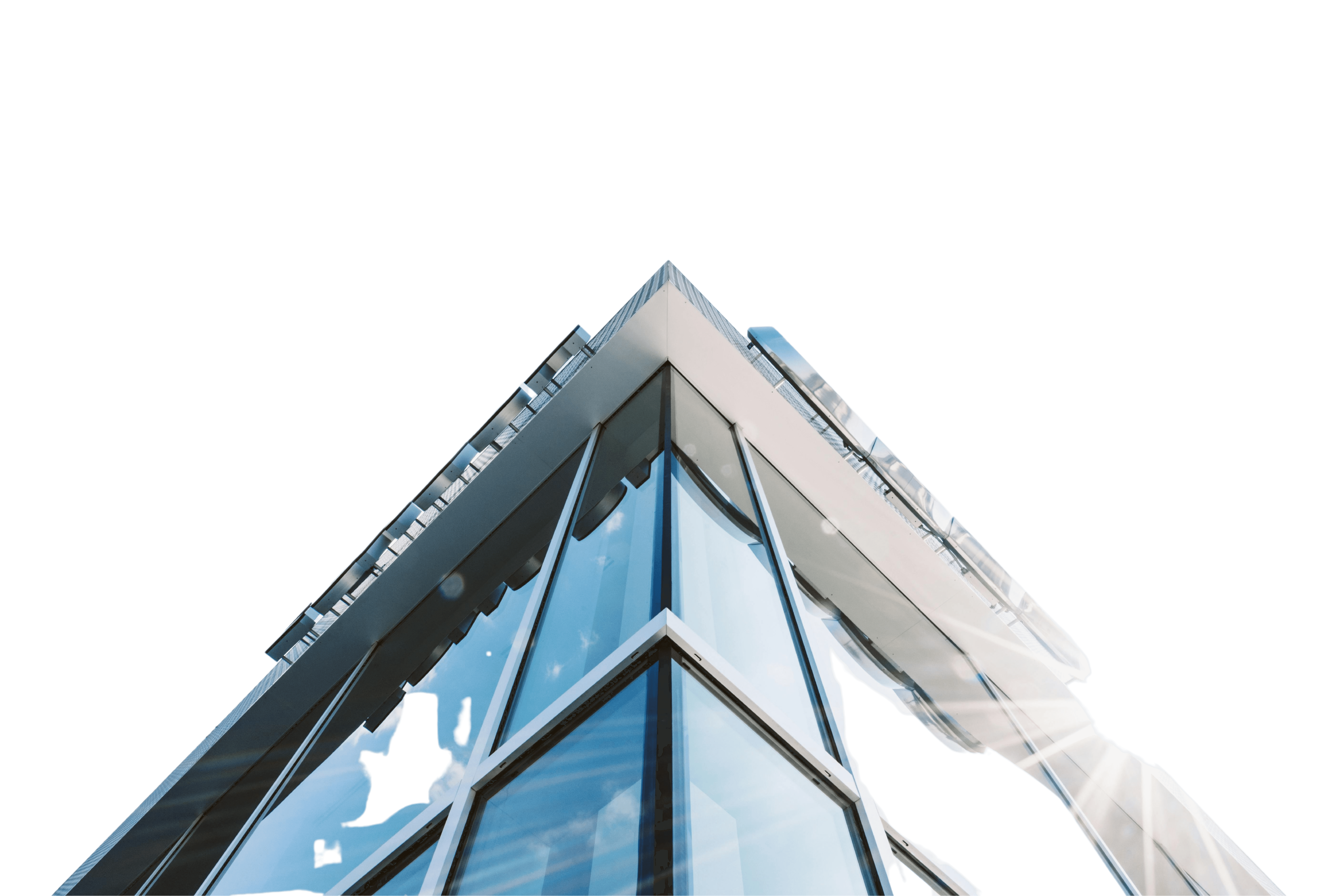
Want the latest information on construction materials?
Subscribe to the Paragon Post
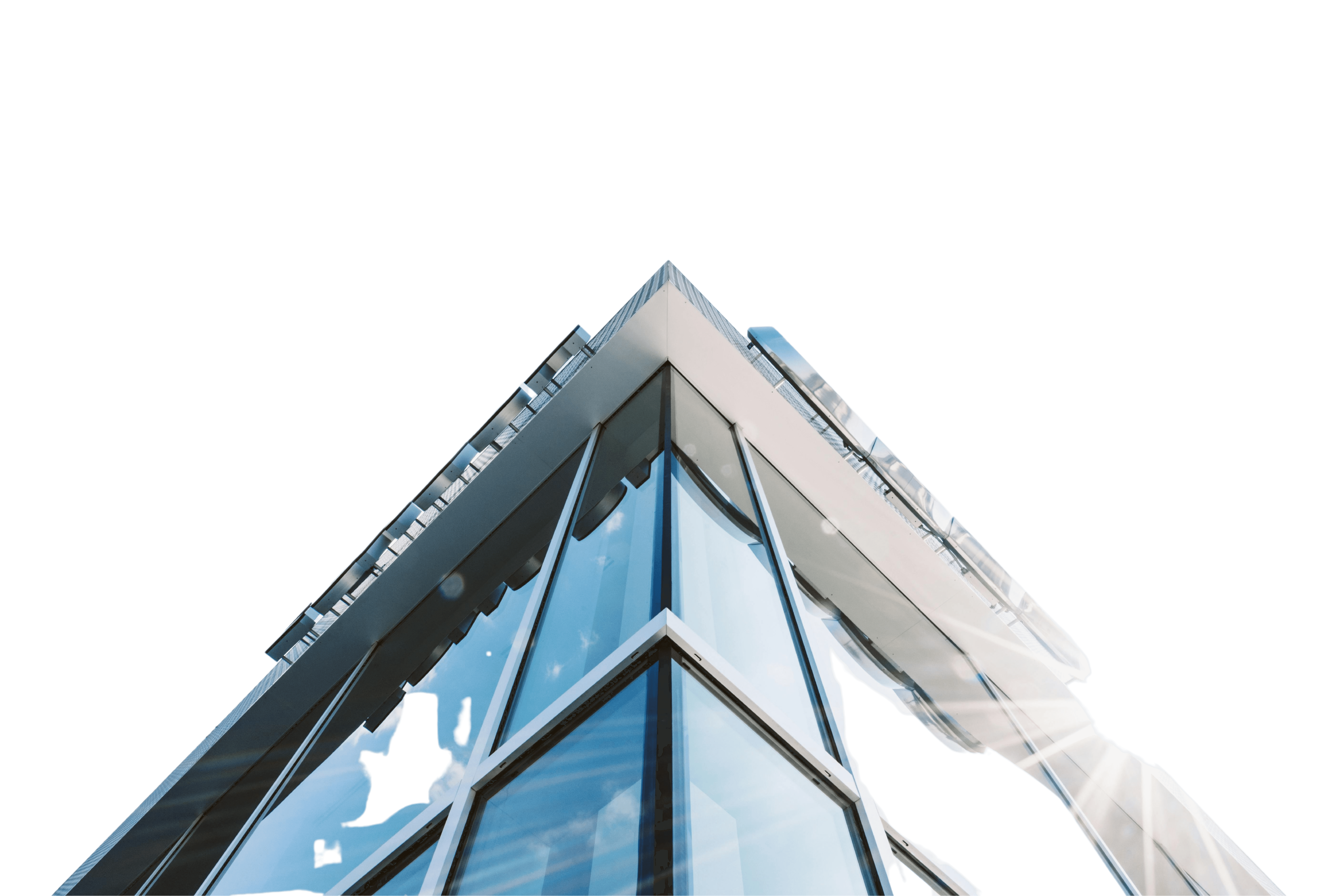
Want the latest information on construction materials?
Subscribe to the Paragon Post
Want the latest information on construction materials?
Subscribe to the Paragon Post


Lumber Prices Surge—Defending Against 2025’s Cost Hikes
Lumber prices surged 17.2% year-over-year in early 2025, reaching $486 per 1,000 board feet, driven by tariff fears, supply chain disruptions, and strong housing demand. Construction input costs are now 40.5% above pre-pandemic levels. Contractors locked into fixed-price contracts face squeezed margins as material costs spike. Proactive strategies such as incorporating escalation clauses, bulk purchasing, and exploring alternative materials are essential to protect budgets. At Paragon, we help clients anticipate these shifts and secure materials early to maintain predictable outcomes amid volatile markets.
Continue reading this article.
“Golden Age” or Tariff-Driven Recession?
ENR’s Top 425 Owners saw construction-in-progress rise 9.3% to $595.8 billion from 2023 to 2024, buoyed by moderately sized projects as megaprojects mature. Yet labor growth is stalling, and President Trump’s new tariffs—up to 50% reciprocal duties on imports from 90 countries—triggered a $5 trillion market loss in two days. University project managers describe adapting to market shifts as “like turning a battleship.” Experts warn a recession may already have begun. Owners are prioritizing early procurement, flexible contracts, and alternative designs to manage rising costs and uncertainty. Paragon helps clients navigate this volatile “golden age” with strategic planning and collaboration.
Continue reading this article.
Wildfire Recovery in Los Angeles
The January 2025 wildfires destroyed over 16,000 structures in Los Angeles, causing up to $54 billion in damage and displacing thousands. Rebuilding faces labor shortages, supply chain constraints, and insurance challenges. Fire-resistant materials like steel and fiber cement reduce vulnerability by 60%, while modular robotics such as Concert accelerate reconstruction and improve safety. Permitting timelines have been cut from 120 to 45 days. Coordinated debris removal and community rebuilding authorities are critical for recovery. Paragon’s disaster recovery expertise emphasizes detailed planning, transparent communication, and flexible phased delivery to build a more resilient future.
Continue reading this article.
Preparing for Recession — How Construction Can Stay Resilient in 2025
Sixty percent of CFOs predict a recession in 2025 amid tariffs, inflation, and rising interest rates. Construction input prices are up 40.5% since 2020, while labor shortages demand 439,000 new workers this year. Firms are adopting phased project approaches, diversified supply chains, and AI-driven cost tracking to mitigate risk. Modular robotics like Concert fill labor gaps by handling repetitive tasks, enhancing safety and efficiency. Anirban Basu cautions tariffs are “medicine” that may strain the industry. Paragon guides clients through scenario planning, flexible contracts, and technology adoption to thrive amid economic uncertainty.
Continue reading this article.
Conclusion
The construction industry in 2025 is facing a series of interconnected challenges—tariffs, rising material costs, labor shortages, and supply chain disruptions—that are more than just obstacles; they’re signals of a fundamental shift. Tariffs on steel, aluminum, and other key materials are inflating prices at a rate not seen in years, forcing contractors to revisit pricing models, renegotiate contracts, and explore alternative sourcing strategies. Meanwhile, automation and AI-driven robotics like Concert are beginning to reshape job sites, filling critical labor gaps and making projects safer and more efficient. At the same time, global trade tensions and domestic policy uncertainties are creating volatile markets, with supply chains strained and costs unpredictable. Every project now requires proactive planning, flexible procurement, and innovative solutions to stay on schedule and within budget. The companies that will thrive aren’t waiting for stability—they’re leading by adapting quickly, leveraging technology, and forging resilient supply partnerships. But perhaps the greatest risk isn’t rising costs—it’s inaction. This is a moment for bold, data-informed decisions rooted in discipline and foresight. The industry’s future belongs to those who see disruption as an opportunity to innovate, to build smarter, and to lead with purpose. At Paragon Construction Consulting, we believe this is a defining moment—one where strategic action and unwavering focus will set the standard for the next generation of construction. Let’s build that future—together.
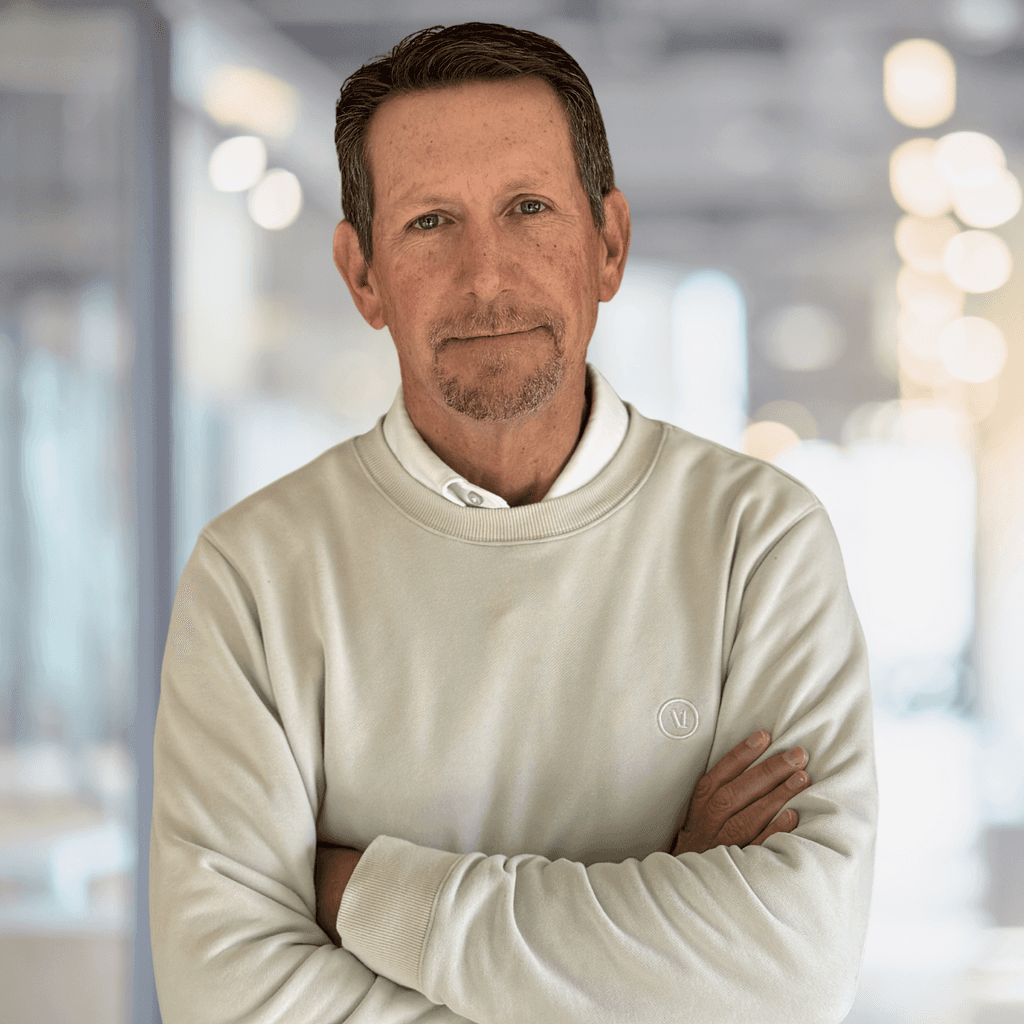
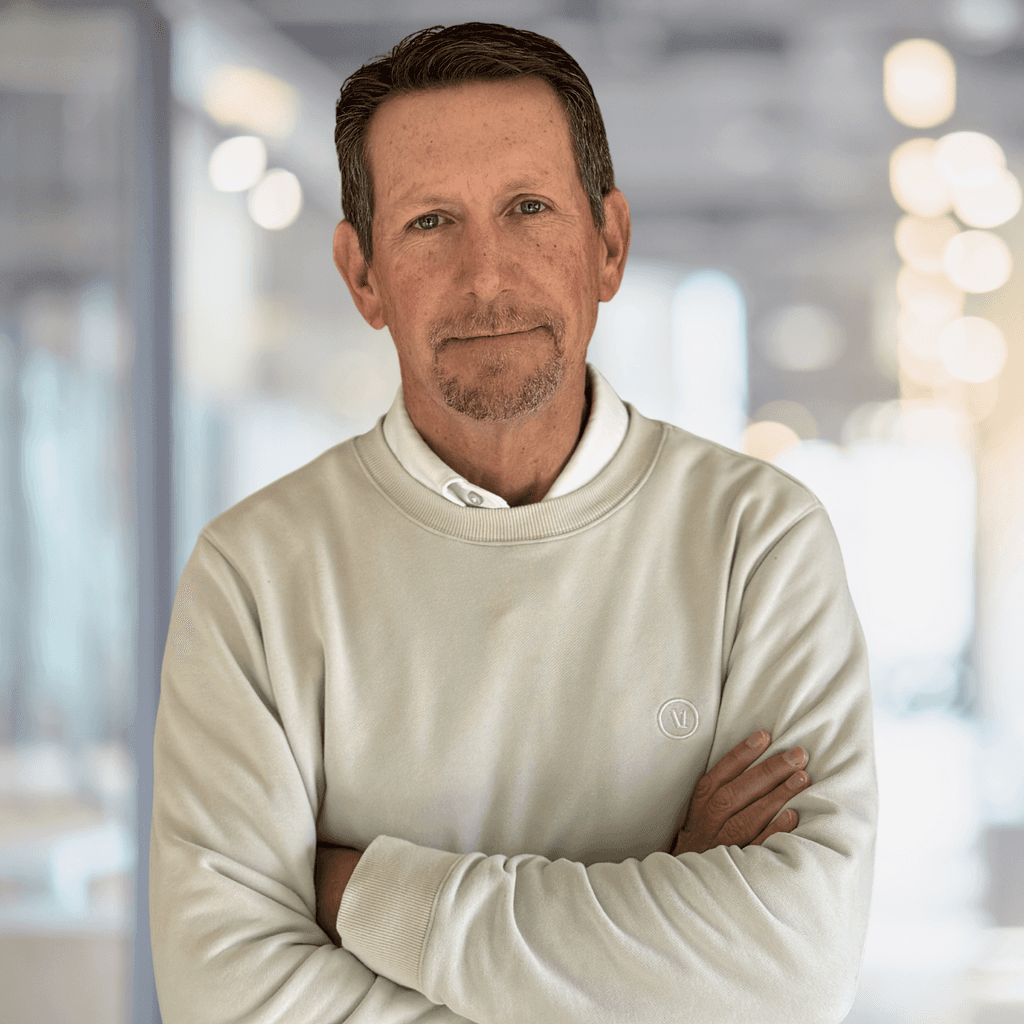
Jeff Hall
President & CEO
Online
Online
Get in Touch
Get in Touch
Commodity
12 Month % Change
1 Month % Change
Softwood Lumber
+12.6
+4.7
Hardwood Lumber
+1.0
+6.6
General Millworks
+0.9
-0.1
Soft Plywood Products
-6.1
+0.6
Hot Rolled Steel
-11.4
+2.3
Copper Wire & Cable
+12.7
+5.5
Power Wire & Cable
+5.2
+2.2
Builder's Hardware
+2.9
+0.6
Plumbing Fixtures
+2.6
0.0
Furnaces and Heaters
-0.4
+0.3
Sheet Metal Products
+1.3
+1.5
Electrical Lighting Fixtures
+3.1
+0.3
Nails
-3.7
0.0
Major Appliances
-0.4
-0.1
Ready-Mix Concrete
+0.5
-0.4
Asphalt Roofing & Siding
-0.6
-0.2
Gypsum Products
+1.8
0.0
Insulation
+5.6
+0.6
Contractor Confidence Crashes Amid Tariff Chaos
Contractor confidence hit a three-year low in early 2025 as tariffs on steel and aluminum drove construction input prices up 1.4% in January—the largest jump in two years. Labor growth slowed to 1.8% year-over-year, the weakest in four years, while 80% of contractors faced tariff-related price hikes and 20% paused projects. Firms are responding with shorter bid windows, stronger supplier partnerships, and real-time cost tracking. Anirban Basu warns tariffs could stall nearly $600 billion in construction-in-progress. Paragon advises agile procurement and risk-sharing contracts to navigate this uncertainty.
Continue reading this article.
20-City Average Cost Indexes, Wages, Prices
ENR publishes both a Construction Cost Index and Building Cost index that reports the average national price by surveying 20 major cities across the United States. These figures report the national average change of cost over the last month.
CONCRETE BLOCK
+1.1%
READY MIX CONCRETE
0.0
ASPHALT PAVING
-0.3
PORTLAND CEMENT
+6.9
ALUMINIUM SHEET
+0.1%
REINFORCING BARS
-1.5%
WIDE FLANGE
+0.4%
STAINLESS-STEEL SHEET
+3.3%
CORRUGATED-STEEL PIPE
-1.2%
DUCTILE-IRON PIPE
+2.5%
PVC WATER PIPE
+0.6%
REINFORCED CONCRETE PIPE
-2.2%
GYPSUM WALLBOARD
-0.3%
PARTICLE BOARD
+1.2%
PLYWOOD
+1.5%
LUMBER
+2.0%
Sources
https://www.enr.com/articles/60154-clayco-dives-deep-into-data-center-construction
https://www.maslon.com/how-the-new-administration-may-impact-the-construction-industry
Paragon compiles the latest and most accurate information. It’s worth noting, some sources release data more or less frequently.
Sources
Paragon compiles the latest and most accurate information. It’s worth noting, some sources release data more or less frequently.
April 2025: Construction Materials Price Report


Lumber Prices Surge—Defending Against 2025’s Cost Hikes
Lumber prices surged 17.2% year-over-year in early 2025, reaching $486 per 1,000 board feet, driven by tariff fears, supply chain disruptions, and strong housing demand. Construction input costs are now 40.5% above pre-pandemic levels. Contractors locked into fixed-price contracts face squeezed margins as material costs spike. Proactive strategies such as incorporating escalation clauses, bulk purchasing, and exploring alternative materials are essential to protect budgets. At Paragon, we help clients anticipate these shifts and secure materials early to maintain predictable outcomes amid volatile markets.
“Golden Age” or Tariff-Driven Recession?
ENR’s Top 425 Owners saw construction-in-progress rise 9.3% to $595.8 billion from 2023 to 2024, buoyed by moderately sized projects as megaprojects mature. Yet labor growth is stalling, and President Trump’s new tariffs—up to 50% reciprocal duties on imports from 90 countries—triggered a $5 trillion market loss in two days. University project managers describe adapting to market shifts as “like turning a battleship.” Experts warn a recession may already have begun. Owners are prioritizing early procurement, flexible contracts, and alternative designs to manage rising costs and uncertainty. Paragon helps clients navigate this volatile “golden age” with strategic planning and collaboration.
Wildfire Recovery in Los Angeles
The January 2025 wildfires destroyed over 16,000 structures in Los Angeles, causing up to $54 billion in damage and displacing thousands. Rebuilding faces labor shortages, supply chain constraints, and insurance challenges. Fire-resistant materials like steel and fiber cement reduce vulnerability by 60%, while modular robotics such as Concert accelerate reconstruction and improve safety. Permitting timelines have been cut from 120 to 45 days. Coordinated debris removal and community rebuilding authorities are critical for recovery. Paragon’s disaster recovery expertise emphasizes detailed planning, transparent communication, and flexible phased delivery to build a more resilient future.
Preparing for Recession — How Construction Can Stay Resilient in 2025
Sixty percent of CFOs predict a recession in 2025 amid tariffs, inflation, and rising interest rates. Construction input prices are up 40.5% since 2020, while labor shortages demand 439,000 new workers this year. Firms are adopting phased project approaches, diversified supply chains, and AI-driven cost tracking to mitigate risk. Modular robotics like Concert fill labor gaps by handling repetitive tasks, enhancing safety and efficiency. Anirban Basu cautions tariffs are “medicine” that may strain the industry. Paragon guides clients through scenario planning, flexible contracts, and technology adoption to thrive amid economic uncertainty.
Sources
https://www.enr.com/articles/60154-clayco-dives-deep-into-data-center-construction
https://www.maslon.com/how-the-new-administration-may-impact-the-construction-industry
Paragon compiles the latest and most accurate information. It’s worth noting, some sources release data more or less frequently.
Sources
Paragon compiles the latest and most accurate information. It’s worth noting, some sources release data more or less frequently.
Commodity
12 Month % Change
1 Month % Change
Softwood Lumber
+12.6
+4.7
Hardwood Lumber
+1.0
+6.6
General Millworks
+0.9
-0.1
Soft Plywood Products
-6.1
+0.6
Hot Rolled Steel
-11.4
+2.3
Copper Wire & Cable
+12.7
+5.5
Power Wire & Cable
+5.2
+2.2
Builder's Hardware
+2.9
+0.6
Plumbing Fixtures
+2.6
0.0
Furnaces and Heaters
-0.4
+0.3
Sheet Metal Products
+1.3
+1.5
Electrical Lighting Fixtures
+3.1
+0.3
Nails
-3.7
0.0
Major Appliances
-0.4
-0.1
Ready-Mix Concrete
+0.5
-0.4
Asphalt Roofing & Siding
-0.6
-0.2
Gypsum Products
+1.8
0.0
Insulation
+5.6
+0.6
Contractor Confidence Crashes Amid Tariff Chaos
Contractor confidence hit a three-year low in early 2025 as tariffs on steel and aluminum drove construction input prices up 1.4% in January—the largest jump in two years. Labor growth slowed to 1.8% year-over-year, the weakest in four years, while 80% of contractors faced tariff-related price hikes and 20% paused projects. Firms are responding with shorter bid windows, stronger supplier partnerships, and real-time cost tracking. Anirban Basu warns tariffs could stall nearly $600 billion in construction-in-progress. Paragon advises agile procurement and risk-sharing contracts to navigate this uncertainty.
Continue reading.
20-City Average Cost Indexes, Wages, Prices
ENR publishes both a Construction Cost Index and Building Cost index that reports the average national price by surveying 20 major cities across the United States. These figures report the national average change of cost over the last month.
CONCRETE BLOCK
+1.1%
READY MIX CONCRETE
0.0
ASPHALT PAVING
-0.3
PORTLAND CEMENT
+6.9
ALUMINIUM SHEET
+0.1%
REINFORCING BARS
-1.5%
WIDE FLANGE
+0.4%
STAINLESS-STEEL SHEET
+3.3%
CORRUGATED STEEL PIPE
-1.2%
DUCTILE-IRON PIPE
+2.5%
PVC WATER PIPE
+0.6%
REINFORCED CONCRETE PIPE
-2.2%
GYPSUM WALLBOARD
-0.3%
PARTICLE BOARD
+1.2%
PLYWOOD
+1.5%
LUMBER
+2.0%
April 2025: Construction Materials Price Report
Conclusion
The construction industry in 2025 is facing a series of interconnected challenges—tariffs, rising material costs, labor shortages, and supply chain disruptions—that are more than just obstacles; they’re signals of a fundamental shift. Tariffs on steel, aluminum, and other key materials are inflating prices at a rate not seen in years, forcing contractors to revisit pricing models, renegotiate contracts, and explore alternative sourcing strategies. Meanwhile, automation and AI-driven robotics like Concert are beginning to reshape job sites, filling critical labor gaps and making projects safer and more efficient. At the same time, global trade tensions and domestic policy uncertainties are creating volatile markets, with supply chains strained and costs unpredictable. Every project now requires proactive planning, flexible procurement, and innovative solutions to stay on schedule and within budget. The companies that will thrive aren’t waiting for stability—they’re leading by adapting quickly, leveraging technology, and forging resilient supply partnerships. But perhaps the greatest risk isn’t rising costs—it’s inaction. This is a moment for bold, data-informed decisions rooted in discipline and foresight. The industry’s future belongs to those who see disruption as an opportunity to innovate, to build smarter, and to lead with purpose. At Paragon Construction Consulting, we believe this is a defining moment—one where strategic action and unwavering focus will set the standard for the next generation of construction. Let’s build that future—together.
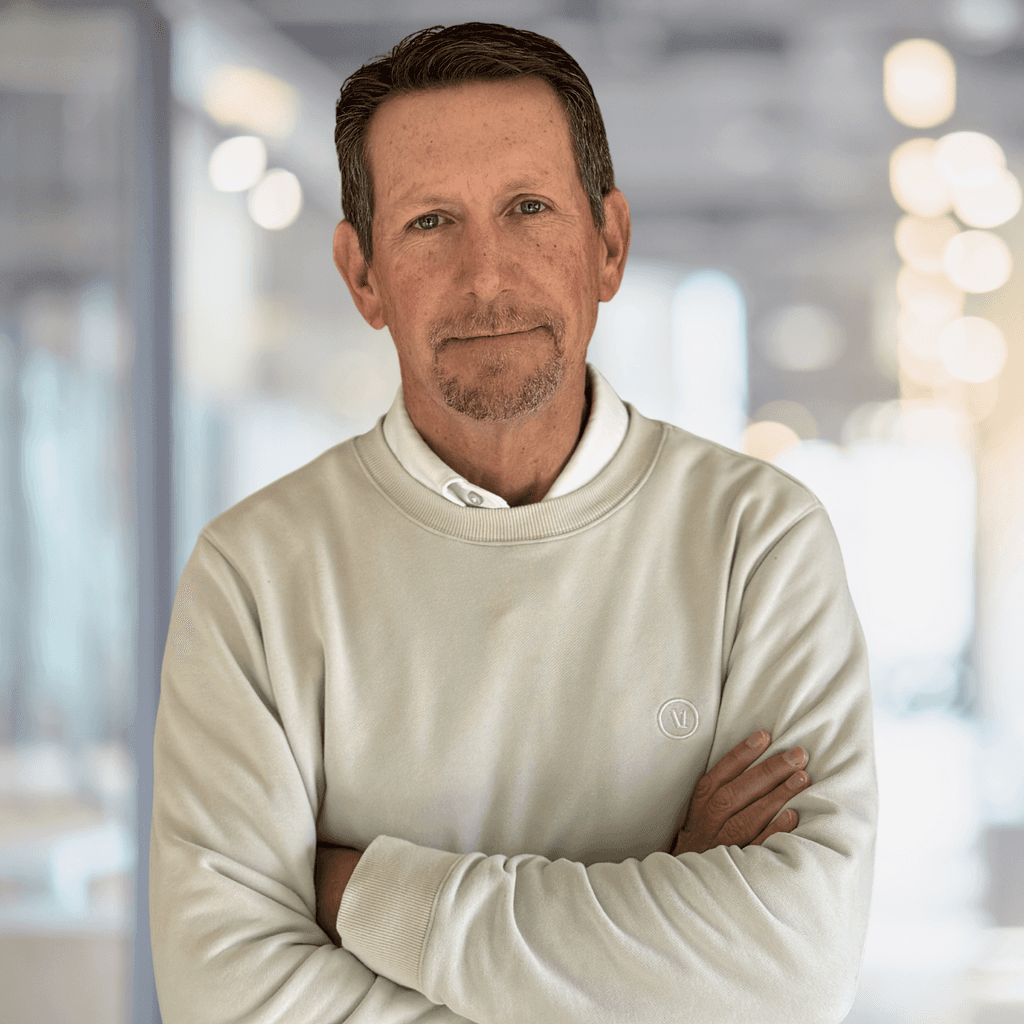
Jeff Hall
President & CEO
Jeff Hall
President & CEO
Online
Get in Touch