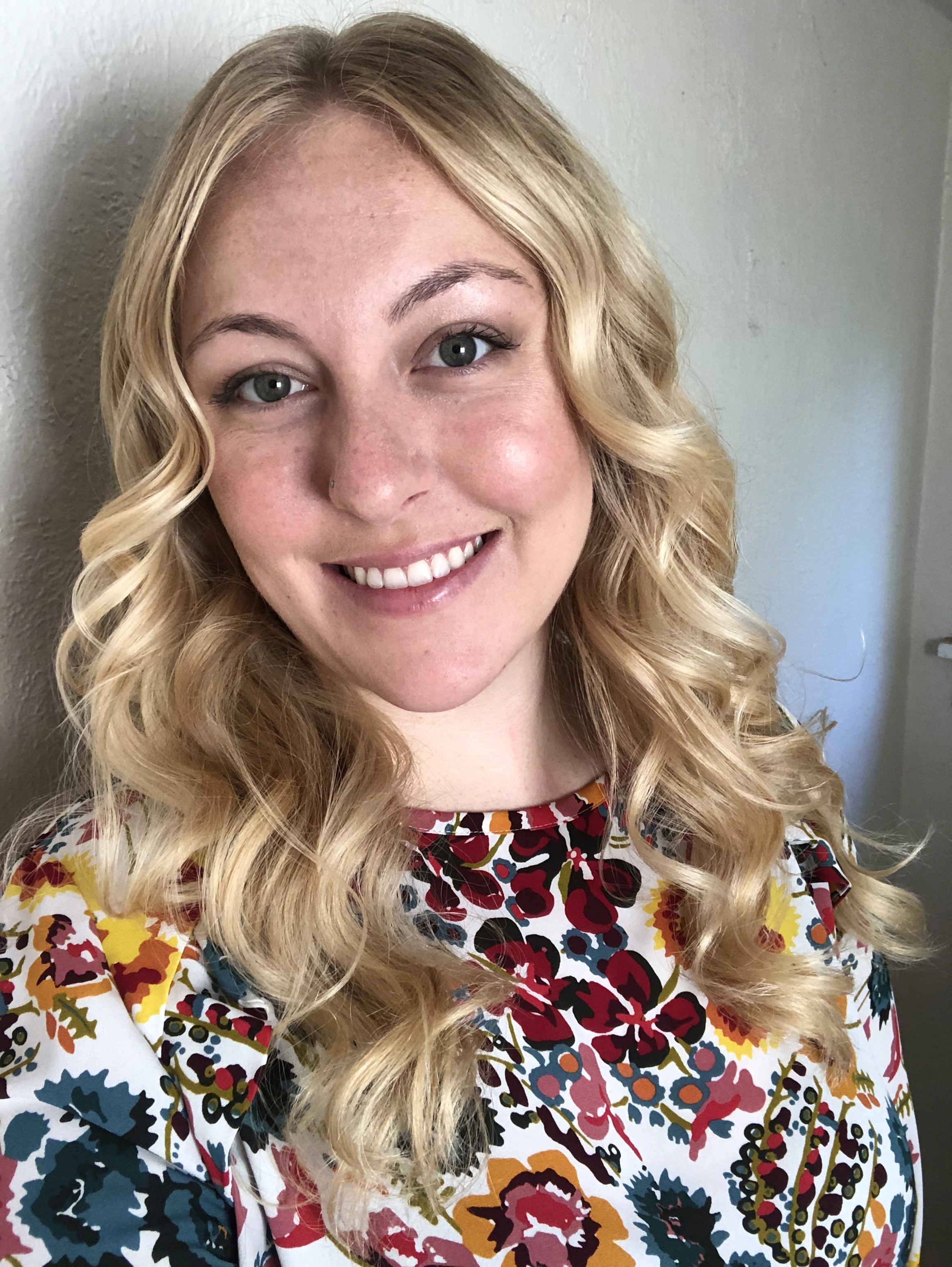
Material prices are on the rise again, and contractors are feeling the pressure. Construction input prices jumped 1.4% in January, marking the biggest increase in two years, according to the Associated Builders and Contractors (ABC).
Why Are Costs Surging?
Several factors are driving this spike. Energy costs have risen sharply, with crude petroleum, natural gas, and other unprocessed energy materials seeing significant increases. Seasonal price adjustments have also played a role, as many suppliers raise prices at the start of the year. However, the biggest driver appears to be fear over impending tariffs.
With the return of steel and aluminum tariffs under the Trump administration, contractors have rushed to buy materials before costs climb even higher. This panic buying has created an artificial surge in demand, driving prices up even more.
The Impact on Contractors
Ken Simonson, chief economist for the Associated General Contractors of America, warns that even the mere threat of tariffs has already led to noticeable price jumps. Contractors locked into fixed-price contracts will be particularly vulnerable, as they’ll be forced to absorb rising material costs without flexibility to adjust pricing.
For the broader industry, the numbers paint a clear picture of concern. Construction input costs are now 40.5% higher than in February 2020, and the trend isn’t slowing down. Supply chain disruptions will make material procurement more difficult, leading to potential project delays and budget overruns. ABC’s chief economist, Anirban Basu, predicts that tariffs will have the most lasting impact, with cost escalation expected to continue through the first half of 2025.
How Contractors Can Protect Their Projects
With material price volatility becoming a growing challenge, contractors need to act now to protect their projects and profit margins.
One of the best defenses is to include material escalation clauses in contracts, ensuring that cost fluctuations don’t fall entirely on the contractor. Strategic bulk purchasing of key materials can help mitigate future price hikes, but it’s essential to balance stockpiling with financial stability. Exploring alternative materials and adjusting procurement strategies can also provide flexibility as prices shift.
Perhaps most importantly, staying informed on tariff policy changes and economic trends will be key to anticipating market shifts. The companies that proactively adapt will be the ones that weather the storm.
The Bottom Line
At Paragon Construction Consulting, we specialize in helping contractors navigate cost volatility, risk management, and contractual safeguards to keep projects on track. With tariffs looming and material prices rising, now is the time to reassess budgets, renegotiate contracts, and implement strategies to stay ahead.
How are you preparing for price increases in 2025? Let’s talk.